The Denim Chronicles
- Annette Stone
- Mar 24, 2020
- 7 min read
One woman's journey through the warps and wefts of her thesis textile: denim.

A DENIM DONATION
"Always design with intention" has been my philosophy as a designer. Whether that pertains to themes of social injustice, minimizing my environmental impact, or weaving personal experiences into my designs, it is important for me to always design with intention.
I'll do a future post discussing why I am doing an eveningwear collection in denim and why I am passionate about it, so keep your eyes open!
Get ready to read about how my senior thesis denim eveningwear collection fabric was almost entirely created in a washing maching!

With the intention to spread knowledge on sustainability and support brands with sustainable initiatives, I reached out to a representative at ISKO Denim at the beginning of this month to see if they would be willing to donate denim to me for my thesis collection. Guess what?! They agreed! I met Sonny at ISKO's New York City showroom and after an hour looking at different samples and qualities, Sonny agreed to put in my order for a total of 50 yards of their denim fabric! Next thing I know, I received an e-mail with tracking and my denim order is on its way to the Fashion Institute of Technology.
WHEN COVID-19 STRIKES
Due to the timeline of the thesis show, it became clear that I would have to spend my designated spring break in New York doing finishing touches on my garments before the judging for the show took place. Therefore, I scheduled a flight home for a long weekend before spring break so I could see my family. The day my fabric was going to arrive, I was supposed to get on that flight home to Los Angeles. Of course, my fabric happened to arrive just after my flight out of New York took off while I simultaneously received an e-mail that in-school classes would be cancelled for the coming week to work out an on-line program. This story ends with me telling you that it has been almost two weeks now since I'd flown to Los Angeles, and I am currently writing this from the desk in my childhood home, now "stuck" until further notice in California.
My beautiful fabric in NYC while I Facetimed in from California:

The next course of action was a valiant feat by my very incredible friends and fellow fashion design colleagues in New York City who not only went back into school to collect the fabric rolls that had arrived, but then worked around their own school classes and internships (which had not yet closed down) to then mail these rolls to my house in California so that my thesis work wouldn't come to a standstill.
Video proof of how fabulous my friends are. This clearly was no easy journey:
Needless to say, a huge shoutout is owed to my fabulous friends Zun, Susan, Brian, and two RA's whom I've never met and did kind things for a stranger! Additionally, a shoutout is owed to the incredible educator Jerry Dellova who was not only a mentor during the Disney Contest I did (see the Apparel tab under Portfolio for details and hopefully a detailed blog post coming in late May), but provided me with Sonny's contact information AND signed for my denim fabric once it arrived at the college.
WASH YOUR HANDS AND WASH YOUR DENIM
Sure enough, the fabric made its way from the producers in Turkey to New York, and then finally, my home in California.
Proof being in the picture, see my puppy, Winnie, giving the fabrics a thorough inspection.

Now that my fabrics arrived, so did my work. One of the caveats to the donation I received was that the only actual yardage they could provide me was in the raw goods. In the world of denim, that means this denim had not only never been washed, but was also shipped to me straight off the loom -no steps were done in-between). Generally, the denim is also really stiff.
These are swatches of the denim pre-washed:
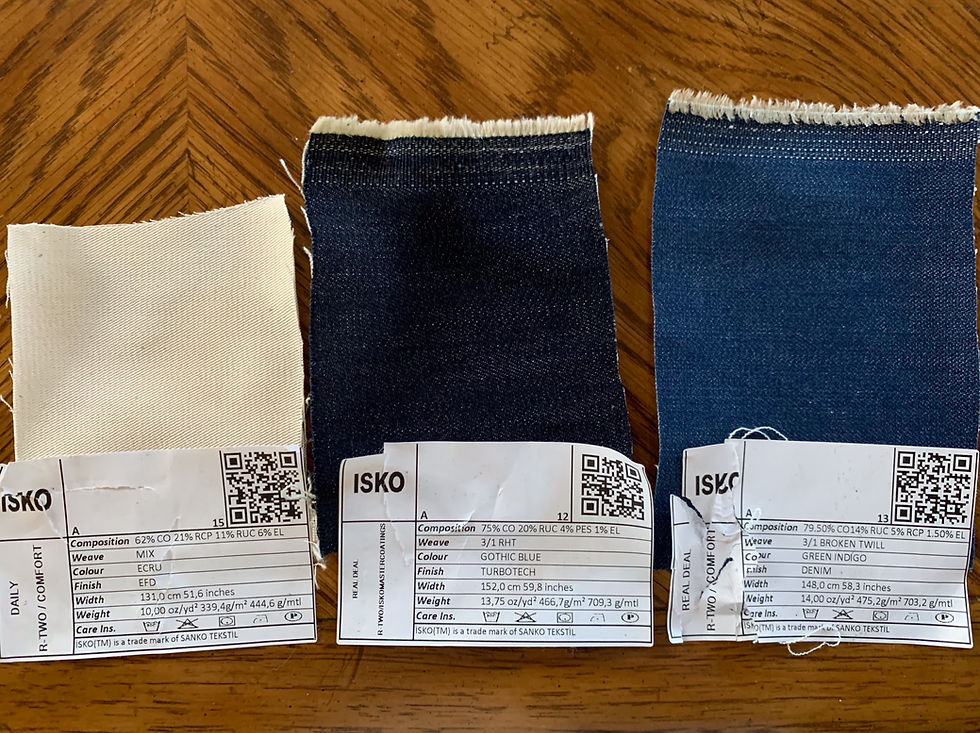
First step: The denim yardage came off the roll and was tossed in the wash with hot water and just a little bit of detergent and then dried in the dryer on high heat. I wanted to ensure maximum shrinkage of the yardage so that in the future if my garments get washed, the wearer won't have to worry about them going down a size!
Post-wash swatches located in the top row:

I found that washing all three bolts of fabric provided enormously positive results not only to the hand ("industry speak" for texture) of the fabric which became much softer, but also to the colors! I had specific swatches I was trying to match the denim color and weight to. They acted as my starting point. The off-white "organic" denim color is for a full denim wedding dress I'm working on and the two blue shades of denim are for my other two looks in the collection. The final challenge with the blue denim is that I needed a third and even lighter shade of the denim. Sonny's showroom was amazing for many reasons, but one particularly helpful reason was that the samples I was looking through not only included the swatch of the raw yardage, but additional swatches of what the raw yardage could wash down to. That is what ultimately lead me to choose these two shades of blue.
A DIFFERENT USE FOR BLEACH DURING THE PANDEMIC
Generally, when bleaching denim, several steps are taken in between washing and bleaching to slowly wear down the color. Since I am at home with limited resources, I elected to jump straight to bleach, but not before inquiring with yet another fabulous educator that I would like to shout out! Introducing Kenneth King, a professor at my college (FIT) known for always going above and beyond for his students and though having limited knowledge in the ways of bleaching denim, he still pointed me in the direction of the bleaching agent I used to ultimately bleach my denim; Rit Color Remover. One precaution to take with massive amounts of bleach is that it tends to ruin the integrity of the fabric. What was/is so great about Rit Color Remover is that it contains a less concentrated quantity of bleach so that my fabric could retain its strength.
(A quick sidebar about Professor King: He is incredibly talented in a multitude of areas including writing and recording videos for Threads Magazine, teaching sewing and patternmaking all across the United States and around the world, having his work on display in multiple museums and galleries including the local favorite Los Angeles County Museum of Art, and he is currently making custom vintage clothing for Barbie dolls! I'll link his website below and you can check him out on Instagram @kennethdking. He always tells his students that the "d" stands for Diva!)
To test the true strength of the Rit Color Remover, I conducted a series of trials in my washing machine. With my dad on chemical rinse duty, and myself stationed at the washing machine as stirring expert, timekeeper, and cutter, we logged 80 minutes of swatches cut every 5 minutes to see how the bleach took to the indigo. That way, when it came to dyeing the yardage I would know approximately how long to keep the fabric in the bleach. What is most interesting is where it becomes obvious that the chemical reaction slows down considerably as time goes on.
Safety first everyone! Safety goggles and gloves:
Below are images that were taken before and after the 16 swatches were dried.
Wet bleach trials:

Dry bleach trials:

I liked the appearances of trials #1 and #5, so the goal was to split the yardage of the lighter raw denim into two pieces, and soak them in the bleach accordingly. The timing wasn't perfect as the quantity made it a lot more difficult to move in and out of the washing machine quickly and slow down the chemical reaction evenly.
Slowing down the chemical reaction of the fabric yardage:

Needless to say, a better plan was worked out for the remaining yardage needing to be bleached!
Next Up!
Once all the fabric was bleached and dried, I cut swatches to complete my final start-to-finish swatch book.
The dyeing process from start-to-finish (The two swatches on the top right are the bleached swatches):

The fabric bleached the lightest definitely did not come out super even because I struggled to slow down the chemical reaction. It best resembles an acid wash appearance. The good news, however, is that most of the denim will be cut into strips and woven together so any uneven tones won't be too noticeable and the parts that are clean and even can be used for pieces that require bigger yardage.
The final four fabrics:

So now that the dyeing process has ended, what's next might you ask? Making my fabric! Now if you have gotten to this point and not clicked off, you must really think I'm crazy. Didn't I just spend almost a week making my fabric? Yes, and no! A majority of this yardage will be cut into strips and woven together and then finally THAT will be my self (outer) fabric. Each of the garments I'm making is lined in silk CDC (Crepe de Chine) and the lining is acting as a structural base with the weaving going overtop.
Denim is one of the most common textiles consumed and worn today. On any given day, about half of the world’s population is wearing denim of some kind. Unfortunately, denim is also one of the world’s most waste intensive and resource-draining fabrications. The dyeing and washing process for denim garments alone contributes greatly to the pollution by the fashion industry. For more information on the fashion industry's pollution, the environmental impact of fashion/textiles, or the impact of denim pollution specifically, I recommend some of the following resources:
The Travels of a T-shirt in the Global Economy by Pietra Rivoli (Book)
Conscious Chatter, Wardrope Crisis, and American Fashion Podcast (Podcasts)
The True Cost (Documentary available on Amazon Prime right now!)
Check out the links below to learn about how you can reduce your environmental impact through clothing:
If you're looking to buy Denim, consider the following companies which I love, support, and appreciate for all that they are doing to reduce their impact on the fashion industry. Check out their initiatives below:
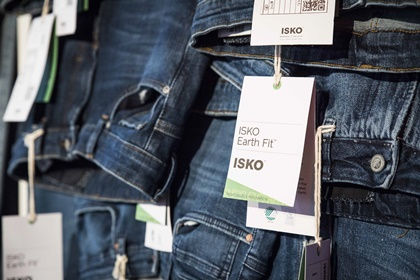
Also, since I'd love to support someone doing some amazing sustainable work, check out my friend Brian's company. If you're a dancer or into dancewear consider supporting this small but growing business:
@rezonanceathletics

By utilizing sustainable sources, donations, and careful shopping, my intention for my thesis collection is to minimize my carbon footprint and industry waste while making a statement that in every clothing category there is a way to be environmentally conscious.
Comments